Технологии производства Парусов
С середины 80-х годов, с развитием вычислительной техники и программного обеспечения, фирмы по производству парусов постепенно компьютеризировались и к началу 2000-х уже все уважающие себя фирмы перешли на компьютерное моделирование и раскрой парусов на плоттере. Это позволило, с одной стороны, упростить и ускорить процесс производства парусов, с другой стороны, систематизировать наработки и значительно улучшить качество выпускаемой продукции.
Самое сложное в «ручном производстве» парусов было то, что парус практически невозможно было повторить. Нет-нет да выложится рейка слегка по-другому, и парус получится не совсем таким, как предыдущий. С применением компьютера и плоттера эта проблема ушла в прошлое.
На данный момент гоночные паруса разделяются на 2-е большие группы: Дакроновые и Ламинатные. Крылья Кубка Америки пока к парусам относить не будем.
Дакроновые паруса с годами практически не изменились; несколько изменились только сами дакроны – они стали более качественные, то есть, при одинаковом весе они стали несколько прочнее и менее растягивающимися. Сейчас паруса из гоночного дакрона в основном используют только на небольших яхтах и на яхтах, где Правилами Класса разрешены только тканые материалы.
На остальных яхтах всё чаще и чаще используют ламинаты, и это связано с тем, что главное для гоночного паруса – это вес и способность держать форму, и ламинаты решают поставленные задачи.
Ламинаты могут быть сделаны по разным технологиям и из разных материалов, но принцип у них всегда один — основа (плёнка, тафета, может быть, даже просто дакрон), усиленная армирующими нитями. Армирующие нити могут быть как из простого полиэстера или из дайнимы, так и из арамидных волокон (Kevlar, Twaron, Technora и т.д.) или из угля. Также ламинатный парус может быть изготовлен из обыкновенного «рулонного» ламината или из «нерулонного» ламината по технологиям D4, Tape-Drive или 3DL/3Di.
«Рулонный» ламинат, по сути, тоже, что и рулонный дакрон, только прочнее и легче, и технология изготовления парусов из него выглядит примерно так же, как и технология изготовления обыкновенного дакронового паруса – те же панели, боуты, швы и т.д.
Значительно интереснее выглядят паруса из «нерулонного» ламината. Сейчас на рынке есть 3-и основных направления (или технологии) по производству таких парусов:
• 3Di – только North Sails;
• D4 – Elvstrom, Quantum, Doyle, OneSails, BankSails и многие др;
• Tape-Drive – UK-Hasley и Doyle.
Технология 3Di — является развитием технологии 3DL, то есть «выпекание» паруса целиком на болване изменяемой формы. 3DL появился в 1992 году, и это был прорыв в технологическом развитии производства парусов. Об 3DL уже много писали, в том числе и в журнале «Катера и Яхты» №2 (160) 1996 г (скан этой статьи можно скачать здесь), поэтому скажем только, что придумала эту технологию и запатентовала её – компания North Sails и, на данный момент, только она производит (и имеет право производить) паруса по технологии 3DL/3Di. Видео процесса формирования и производства 3DL — здесь. Как уже говорилось 3Di – это развитие технологии 3DL. С одной стороны принципиально в ней нет ничего нового – 3Di паруса «выпекается» на том же болване изменяемой формы, что и 3DL паруса. Но, с другой стороны, 3Di паруса собираются не из плёнок и непрерывных нитей, а послойно из специально изготовленных лент. Видео про производство 3Di — здесь и здесь.
Технология D4 появилась в 1996 году, в качестве ответа технологии North 3DL, благодаря усилиям австралийской компании Fraser Sails. История создания этой технологии – здесь, и на русском языке — здесь.
Основная идея паруса изготовленного по технологии D4 – это парус, изготовленный из нескольких ламинированных плоских панелей, где в каждой панели армирующие нити расположены примерно по главным напряжениям, возникающим в парусе под нагрузкой.
Процесс производства панелей D4 и парусов из этих панелей выглядит следующим образом:
1. При проектировании паруса, на нём сразу проектируют (располагают) силовые армирующие и стабилизирующие нити в том количестве, в котором они будут затем выложены на панелях.
2. Далее парус ещё на компьютере разделяют на панели, ширина панелей зависит от «станка» на котором они будут изготовлены.
3. Затем панели расчётно разворачивают на плоскость и отправляют в изготовление на «станок». «Станок» по изготовлению D4 панелей представляет из себя смесь огромного плоттера и пресса.
4. После того, как каждая панель паруса индивидуально будет изготовлена, парус собирают по обыкновенной панельной технологии. (или ультрозвуковая сварка, или обыкновенное сшивание и т.д.).
Как уже говорилось, количество панелей паруса определяется «станком» и/или технологией «станка», на котором эти панели были изготовлены. Обычно небольшие паруса (примерно до тонника/полутонника) изготавливаются из 5-6 панелей, и, соответственно, форма в них задается 4-ю/5-ю швами и серпами по шкаторинам. Большие паруса, изготовленные по технологии D4, чтобы не получать огромные закладки в швах и большую «гранёность» паруса в целом, дробят на более мелкие панели, примерно с шагом 1,5 метра.
Основной смысл этой технологии в том, чтобы нанести на готовый панельный парус непрерывные армирующие силовые ленты. Это так же, как и D4 позволяет сделать парус легче и прочнее.
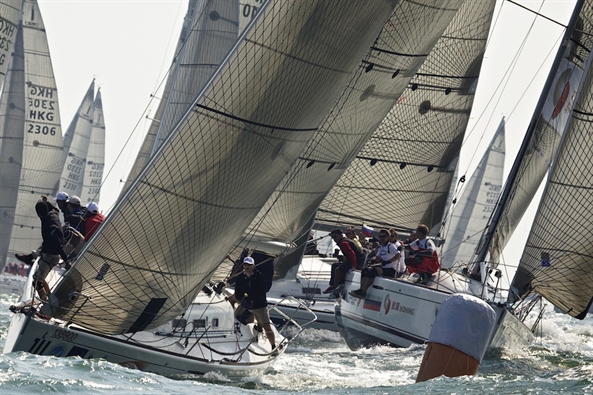
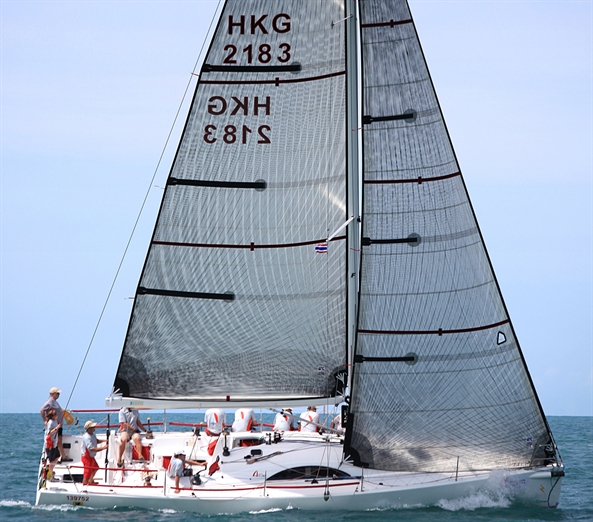
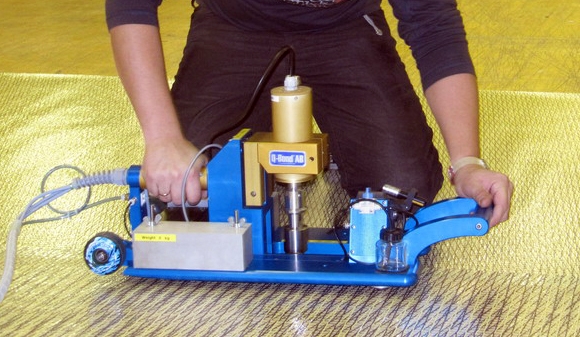